
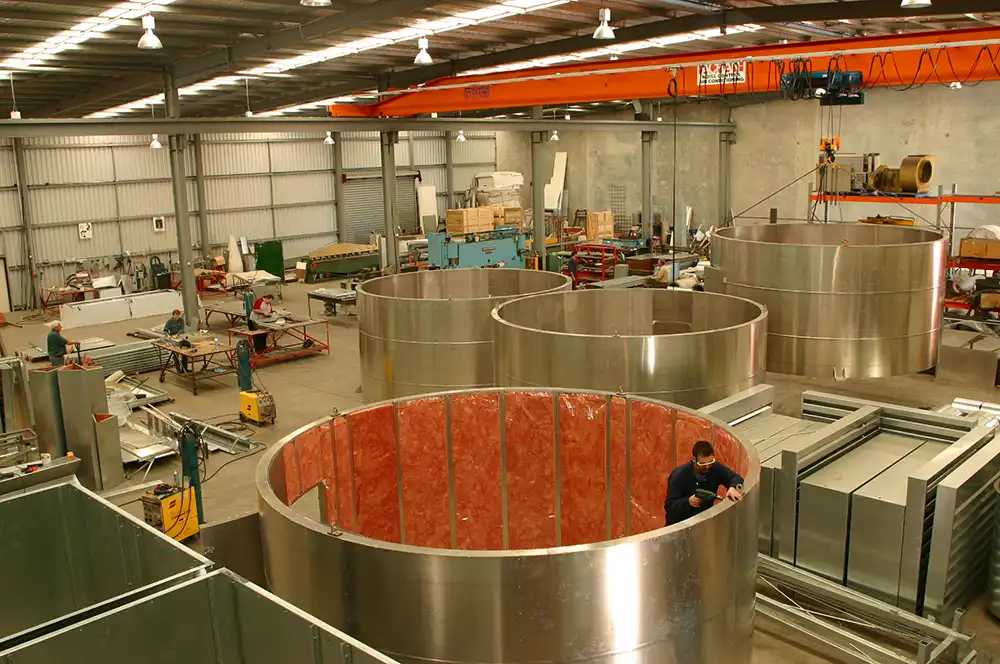
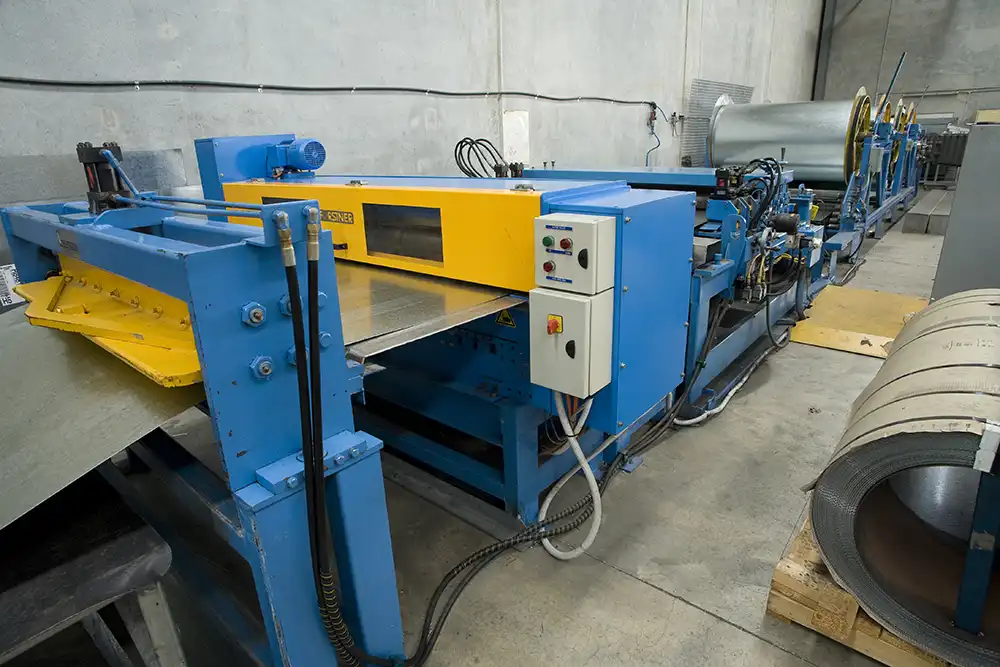
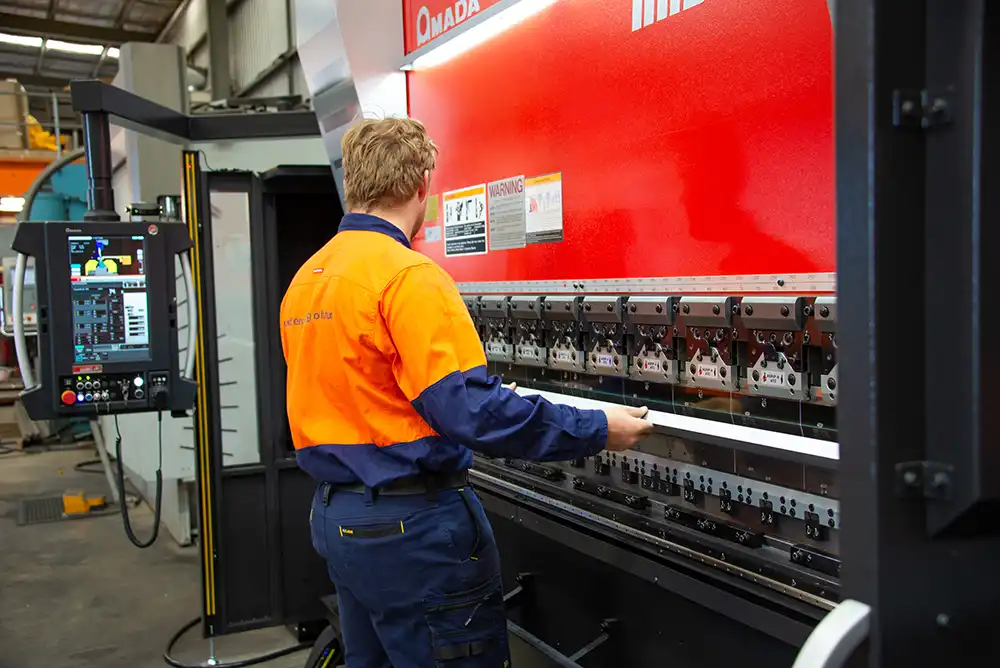
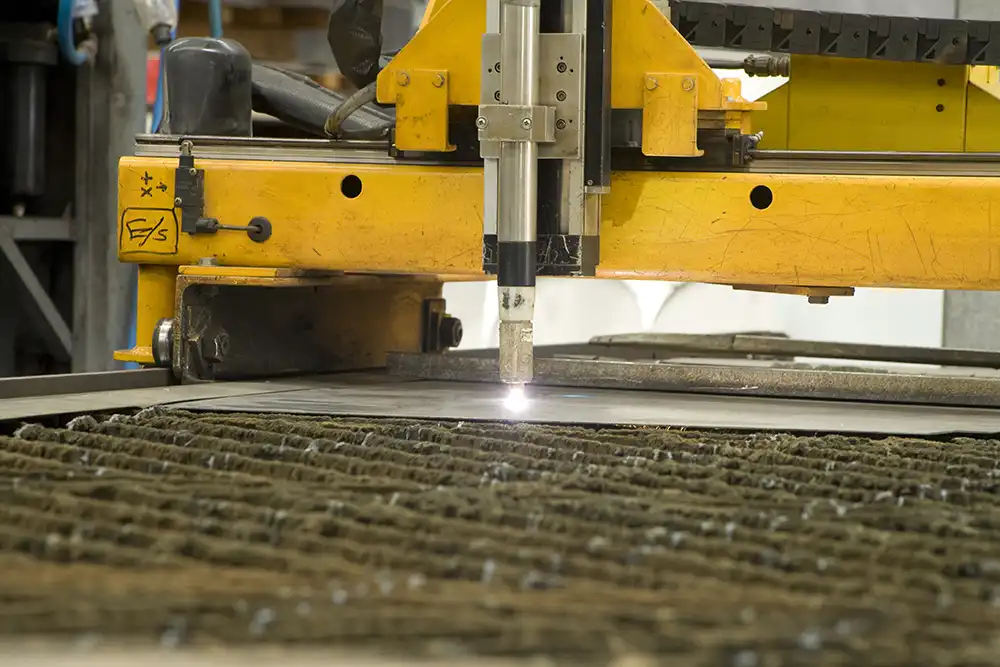
Manufacturing Facility
Acran Sound Control's purpose built 2200m2 facility is located in Brisbane's western suburbs, 12km from Brisbane's CBD with excellent access to South East Queensland's major arterial roads. The building includes both production and assembly areas with a 25m clear span serviced by an 8 tonne overhead crane.
Our CNC manufacturing machinery includes a coil slitting, notching and blanking line, water cutter, computerised press brake, and 135-tonne press brake. These items are supplemented by a traditional array of metal processing equipment.
Acran Sound Control's philosophy has always been to undertake as much manufacturing and assembly work as possible within our facilities to minimise on site erection and assembly time.
Closer supervision of workshop labour ensures superior workmanship at a reduced cost to the client.
The manufacturing process is complemented with state-of-the-art CAD/CAM technology used to provide accurate and consistent parts ready for assembly. This ensures our acoustic products including acoustic louvres attenuators, acoustic doors and enclosures are all manufactured to meet the strictest of customer requirements.
Our facility also allows sufficient space to manufacture an entire set of ventilation and filtration modules for a Dragline.
The manufacturing facilities include the following integral equipment:
- Overhead downshop gantry crane with 25 metre span
- Computerised press brake
- Automated water jet cutter
- Computerised iowa coil line
- Multi gang gauge metal slitter
- Powder coating facility
- Acoustic test facility to provide testing to Australian Standards
- Guillotining
- Folding
- Welding
- Capacity to operate and test up to 150kWr air conditioning equipment for factory acceptance testing and procedures
We welcome existing and future clients to visit our plants by arrangement.
Contact our team Contact our team